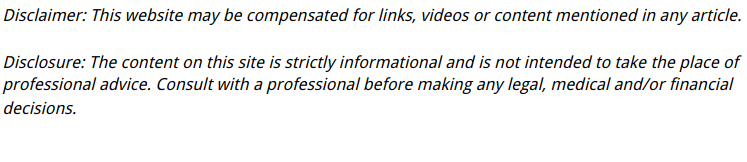

If you’re in an industry where important things are made, then a great way to save time, money, and maybe even lives is to do an assembly analysis of your product. Assembly analysis can take many forms, but our favorite method adapts Eugene Bardach’s path to decision making. The adaptation is below:
Step 1: Define the goal and the assembly process.
This may seem obvious, but you would be surprised how many assumptions can be made especially among smart engineers in a large industry. One person may have a mental image of making a car whose first priority is safety for example, whereas another member of the assembly team might have the idea that the car is being built primarily for speed. Getting everyone on the same page about what the purpose of the assembly process is and how it will be done will set one up for conducting a good assembly analysis.
Step 2: Assemble all needed information and research.
If you need specs on non destructive testing or x-ray inspection pricing before assembly begins, get that information. If you need market research on different kinds of cars and their reverse engineering reports, have that on file. Knowledge is power, especially when you’re creating something out of nothing.
Step 3: Know your alternatives.
You can’t start a sentence with “I should have” if you don’t even know what could be possible. Therefore, a good assembly analysis depends on knowing one’s options. Is motor A faster than motor B, and if so, what makes motor B faster? That expensive NDT test you ordered with the seconds-fast 3D imaging technology and the 2.88 resolution isn’t worth anything if you have no frame of reference.
Step 4: Select and prioritize your criteria.
This kind of goes back to defining the goals of your process, but here you can get really nitty gritty and can quantify what’s important to you and your team during the assembly process.
Step 5: Project the outcomes of your assembly process.
This part is flexible. You could choose to simply project how many prototypes per week you’ll generate and where that will put you from a financing perspective, or you could take a broader view and attempt to project sales. The important part is that you consider what the outcomes are in relation to your different alternatives and weigh the costs and benefits.
Step 6: Confront your trade-offs.
There is no such thing as the perfect machine. Sometimes, speed must be sacrificed for comfort. Other times, efficiency must be sacrificed for beauty. Be aware of the trade-offs involved in every possible assembly decision. Quantify them if possible. Write them down. Figure out how to talk about them, both to your superiors and to the public.
Step 7: Assemble your product!
After doing all these things, you should be ready to go ahead and start the assembly line.
Step 8: Monitor the results–aka, analyse!
After you make and roll out your product, it is important to keep track of efficiency from a financial and mechanical perspective, product safety, and customer feedback. This data will then become a part of the evidence assembly phase in step two the next time you have to make a similar product.